Cruise ships today feel like floating cities, and their design is an incredible feat of creativity, engineering, and problem solving.
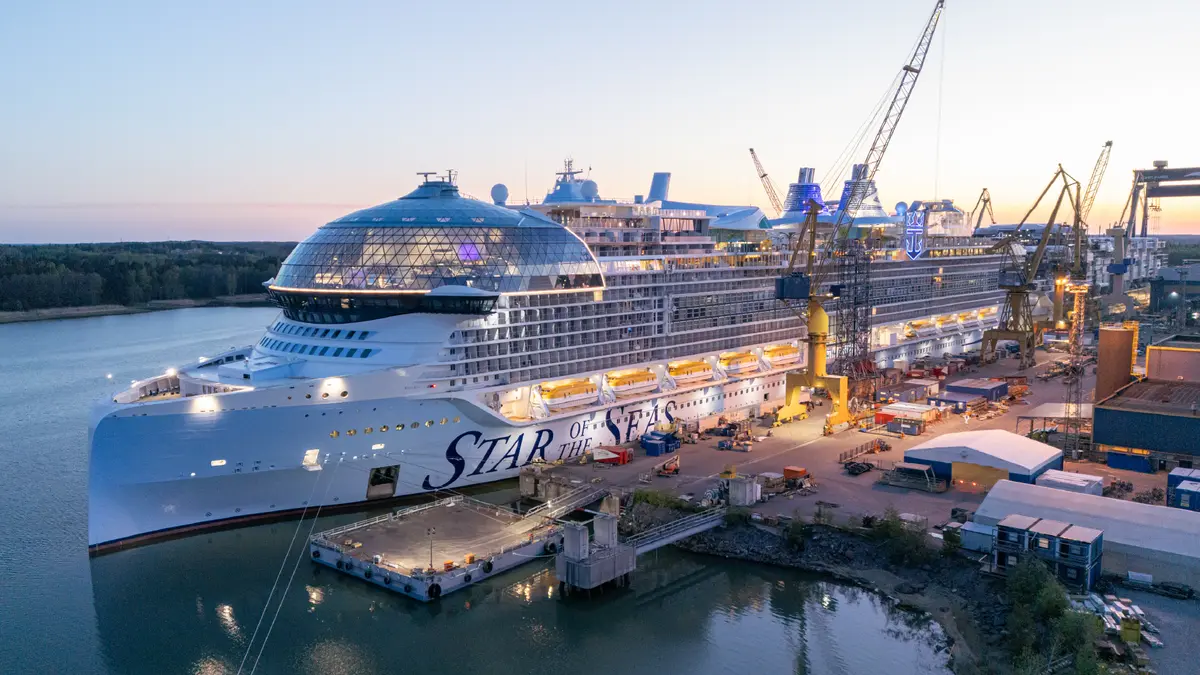
Royal Caribbean employs an army of people to bring a ship to life, and you might be surprised to know one of of their best partners in this process is an architectural firm based in Boston, Massachusetts.
Wilson Butler Architects (WBA) has worked for almost three decades to help Royal Caribbean push the boundaries of what is possible aboard a ship.
With the launch of the second Icon Class ship on the horizon, it's a good reminder how much work goes into these ships.
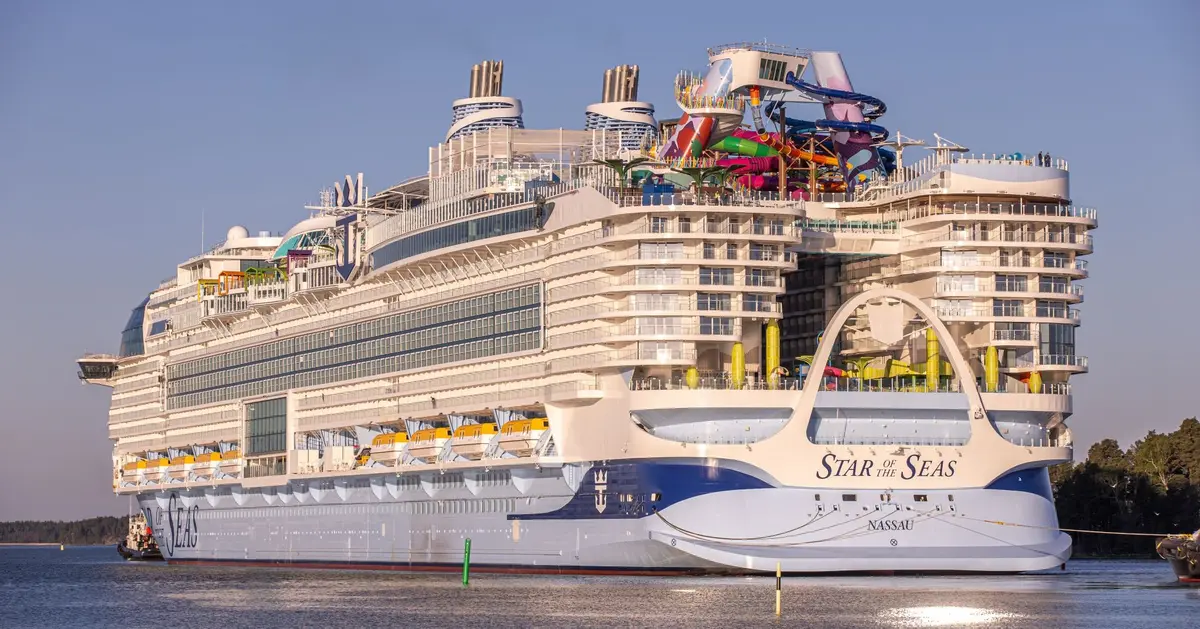
The scale and complexity of building ships like Icon of the Seas or Oasis of the Seas is incredible. New ships can take almost a decade to go from concept to launch and involve the coordination of thousands of professionals across continents. WBA's involvement begins often with a blank page and a single question: What could this ship become?
"We don’t come in after the design is underway," said A. Scott Butler, co-founder of the firm. "We’re at the table at the start, working with Royal Caribbean's Newbuilding & Innovation, along with their product development team, asking what this ship needs to be five years from now."
Helping design over 50 ships
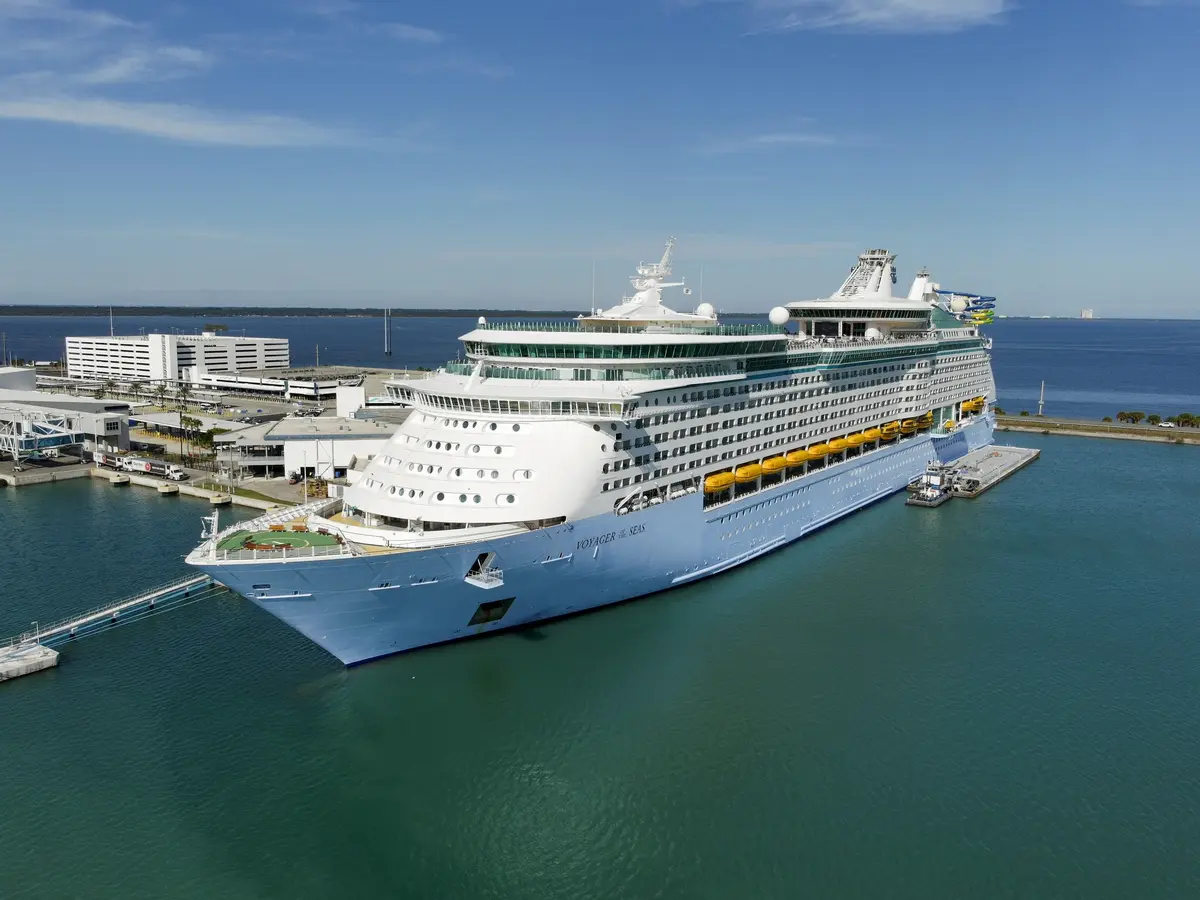
WBA has designed fifteen prototype ships and contributed to 54 vessels across multiple Royal Caribbean Group brands, with seven more in progress.
Their reach spans Voyager Class through Quantum and Icon Class, and the team of Wilson Butler Architects has been involved in many firsts. Among them:
- The first full-scale theater with orchestra pit and fly tower at sea (Voyager of the Seas, 1999)
- The first real-ice skating rink on a cruise ship (Voyager of the Seas, 1999)
- The first live plant park aboard a ship (Central Park, Oasis of the Seas, 2009)
- The tallest slide at sea (The Ultimate Abyss, Harmony of the Seas, 2016)
- The largest glass dome at sea (AquaDome, Icon of the Seas, 2024)
- The largest kinetic sculpture at sea (The Pearl, Icon of the Seas, 2024)
Designing ships is a lot like urban planning, "You’re designing for density, for movement, for delight," said Principal Ben Marcionek. "We think in terms of districts, transit, intersections, light, and rhythm."
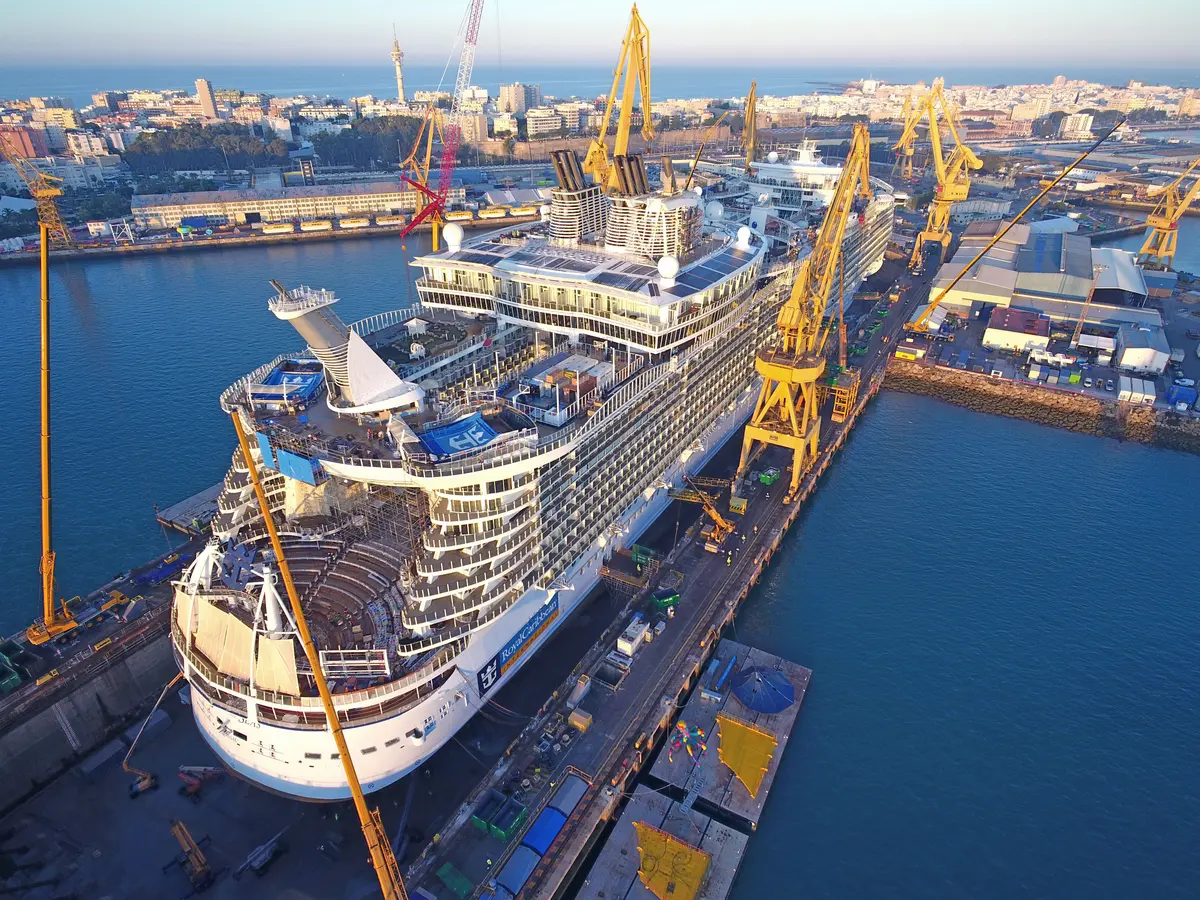
One of their most influential breakthroughs came in 2009 with Oasis of the Seas, which redefined ship architecture by splitting the central structure to allow open-air courtyards and “neighborhoods.” This innovation resulted in now-iconic spaces like Central Park and the Boardwalk.
"That split-hull design gave us the ability to bring daylight deep into the ship," said Butler. "It wasn’t just a stylistic choice—it changed how people interact with the space. Suddenly you could have a real park on Deck 8."
From steel to storytelling
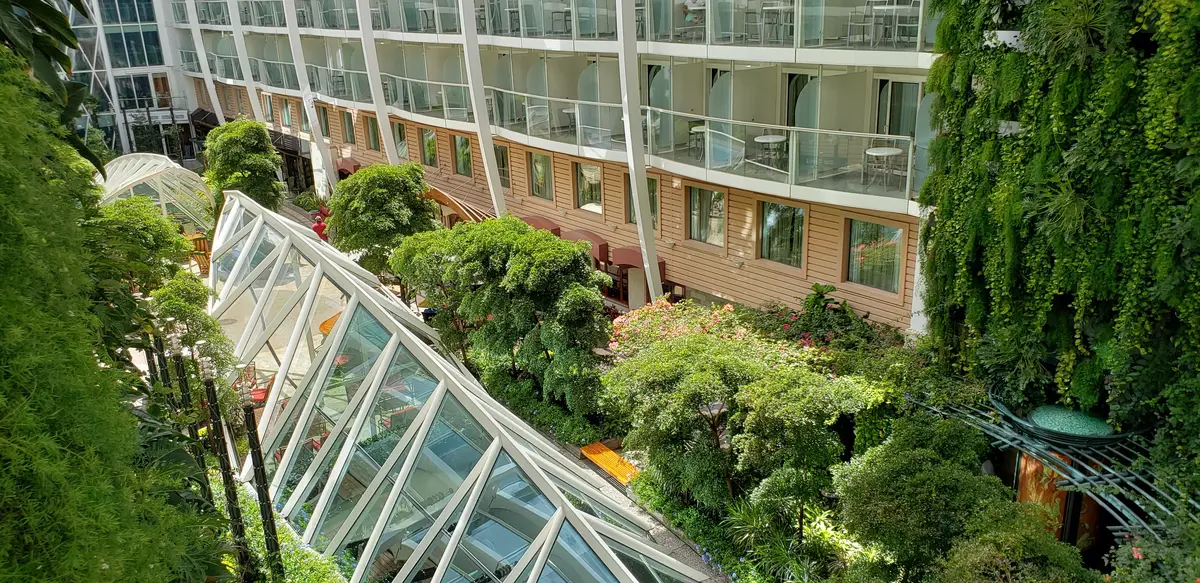
The process of building the world's largest ships begins years before any physical construction begins. Working in concert with engineers, naval architects, acousticians, and outfitters, WBA helps define the experience, not just the structure.
Ship design includes physical models, virtual simulations, and, increasingly, immersive design tools. "Sometimes we’ll build scale models out of basswood to illustrate structural proposals, or we’ll create foam core tray models to show the vertical relationship of venues," said Butler.
Each space is developed with a dual mandate: create something novel, and ensure it functions under extreme conditions—movement, salt air, vibration, and code compliance.
"We’ve had to ask, how do you create an ice rink at sea? How do you build a three-story theater with aerial flying on a moving platform? There’s no textbook for this," Butler explained.
Building ships offers unique opportunities that set it apart from land-based architecture
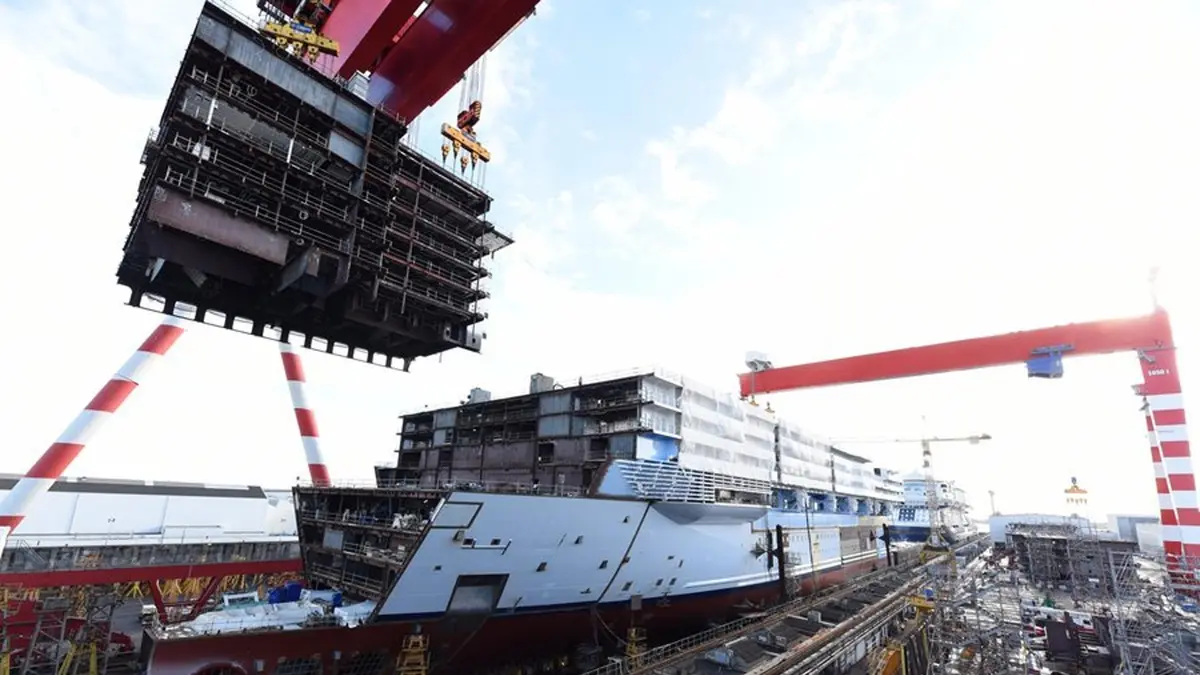
Unlike land-based construction, cruise ship building is modular and sequence-dependent. Hull blocks are prefabricated offsite and welded together like a block puzzle. Every component of each block must be coordinated before the module is craned into position.
This is a challenging approach given how little room there in the building schedule to make changes later, "There’s no field adjustment,” Butler noted. "You can’t just move a beam or a sprinkler without impacting an entire assembly process of every small part."
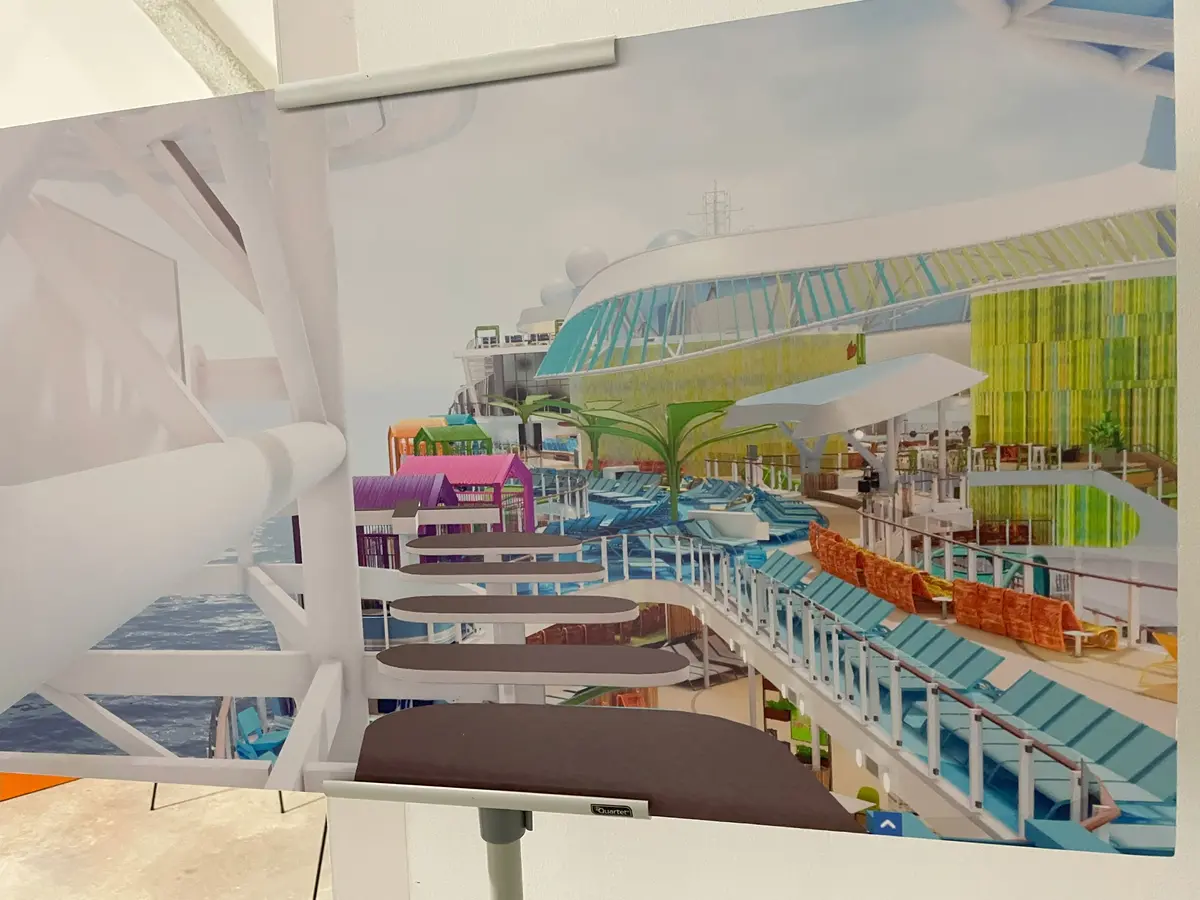
"Our drawings are not just conceptual. They guide fabrication," said Marcionek. "We often produce 1:1 mockups of seating, lighting, or entry transitions to see how they work in real life."